A coffee with… Nacho Moreno – Supply chain logistics & transformation specialist at AIRBUS GROUP
Empack: Tell us, after more than 16 years of professional career within the Airbus Group, what do you think are the biggest differences/challenges that the group has faced in the logistics field if you look back in this professional career?
Nacho: Looking back, during all this time, the change has been, and is being enormous, in a process in which logistics has gone from being considered as NON CORE in the Airbus business, to having a capital importance and being part of the Airbus CORE, because of our own manufacturing process.
We have gone from having a fully delegated logistics, based on external systems and external to the company, mainly reactive and without real control of the data, to a model of ownership of the data and of all the systems in use in the logistics flow.
Within the Digital Logistics Transformation strategy, owning systems that generate quality data is of vital importance to be able to make decisions based on them, optimise processes and reduce inefficiencies, as well as increase visibility in real time.
We are probably halfway down that long road, where we are already generating quality data of our own, and we need to get even more benefit and better results from that data, more automation of processes and tasks, applying artificial intelligence capabilities, IoT, to work more predictively in all areas.
Empack: What does it mean to be a Logistics Transformation Specialist within the company and what is your day-to-day work like?
Nacho: Mainly working on the definition and implementation of standards and innovation in processes, methods and tools within the supply chain. Mastering, controlling, optimising end-to-end (E2E) processes and tools, driving improvement projects by performing flow analysis, cost analysis and calculations, and elimination of non-value added activities, thus contributing to the implementation of the most optimised logistics solution.
Being part of a transnational and multidisciplinary team, acting as a focal point within the Airbus Commercial perimeter in Spain, on the one hand, it is necessary to provide experience and support to the different plants and hubs of the Spanish perimeter, for the implementation of “Top-Down” projects and initiatives promoted from the head office, for the standardisation or homogenisation in processes, methods and tools of the supply chain. On the other hand, it is also necessary to bring local initiatives, detailed knowledge and improvement actions carried out in the Spanish perimeter closer to the central teams for the definition of standards in processes, methods and tools in order to update them, include them in the company’s “catalogues” and/or in the best practices that could be implemented in other centres in other countries.
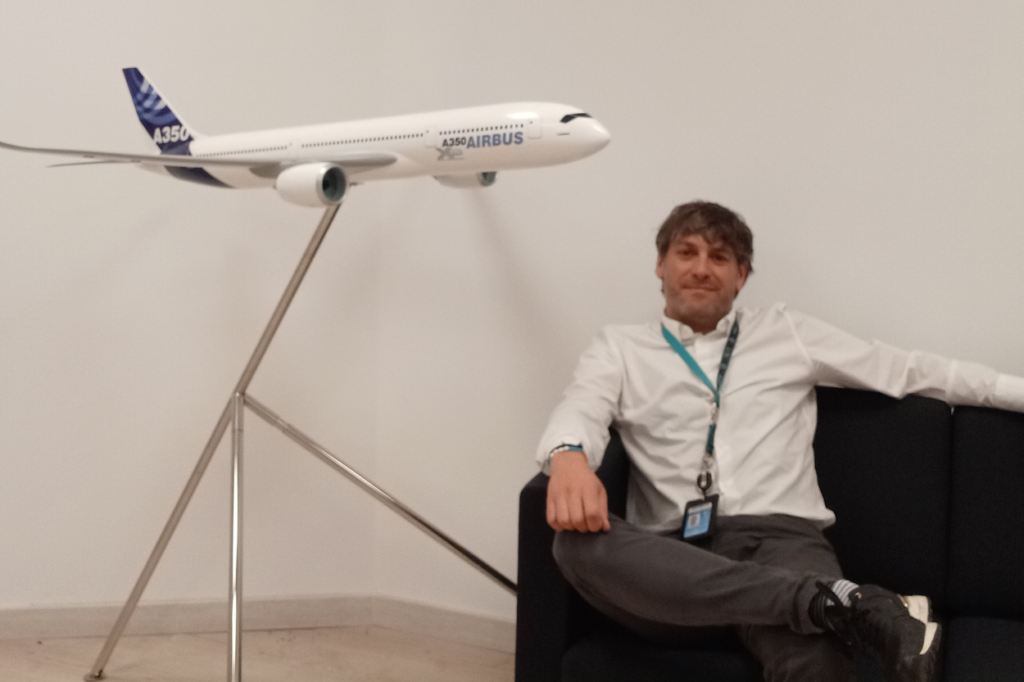
Empack: In terms of sustainability, what are Airbus’ environmental commitments and how do they affect the logistics department, how do you work to reduce your footprint on the planet?
Nacho: Sustainability is a priority issue for Airbus, being present in the personal objectives from the highest management level to any workshop or office employee, and being one of the main axes highlighted in the company’s Vision 2030. We have a multitude of initiatives, ranging from major projects such as CO2 reduction through the use of sustainable aviation fuels or increasing energy efficiency in the plants, to, for example, the creation of volunteer sustainability ambassadors to raise awareness of sustainability issues or promote specific initiatives within the teams around them.
In the logistics area, of course, carbon footprint reduction is a TOP objective, both on a personal and intra-departmental level, and in this regard, we have numerous initiatives, both at transnational and local level, such as Packaging into Motion (PIM), Boomerang Project, Flight to Zero Waste, to name but a few, aimed at reducing wood, cardboard and plastic waste, optimising storage areas and improving logistics flows. In collaboration and coordination with our material suppliers and our logistics service provider (Kuehne+Nagel), we have established a reusable packaging plan that avoids the use of single-use and non-returnable packaging.
Likewise, with our logistics transport provider (DHL), we have established a sustainability strategy and roadmap for the reduction of CO2 emissions, in line with the principles established in the United Nations Global Compact, through the optimisation of transport routes and the improvement in the typology of vehicles and consumption.
Empack: What do you think are the greatest advantages of having trade fairs such as Empack and Logistics & Automation for our industrial fabric?
Nacho: This type of fairs are of great importance when it comes to establishing quality business relationships, and they are a boost to innovation and knowledge. The fact of bringing together many of the most important companies in the sector in the same place makes it possible to share and exchange experiences, learn about the best industry practices that are currently being carried out, obtain direct feedback on products and services, expand business opportunities by building more direct relationships, and get to know in a concentrated way the market trends that can be applied in the not too distant future.
On this point, the evolution towards a format with proposals based on the experiential aspect and content, with very interesting results for the participants, is very noteworthy.
Share this article
Subscribe to our newsletter
Innovation or re-evolution in the packaging sector?
Sugar cane and bamboo, two materials with sustainable properties, are gaining prominence for their reduced environmental impact and renewable benefits. The world of packaging is
Packaging: Sense – Sensibility – Desire
with the support of: Packaging begins and ends with the brand and therefore plays an important role in value creation. Packaging strategy should not only
Un café con… Marta Puyuelo, Corporate Affairs and Sustainability Director en PepsiCo
Empack: Marta, tell us a little bit about your day-to-day life in the company and what your role is at PepsiCo. Marta: It’s difficult for
Coca-Cola removes ‘Sprite’ labels in pilot test for UK market
The Coca-Cola Company is conducting a pilot trial in the UK with the launch of a limited batch of de-labelled packaging for its Sprite and